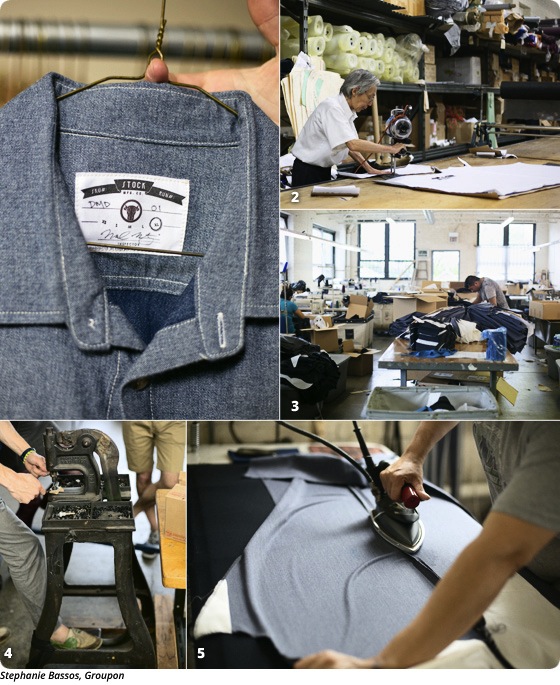
About the last word that comes to mind when you hear "Chicago factory" is "fashionable." But the five men in charge of
Stock Manufacturing Company are aiming to change that. Inside a weathered building in Garfield Park, Jim Snediker, Jason Morgan, Tim Tierney, Mike Morarity, and Areill Ives are developing and producing clothes to sell through their online store. Jason says he and his partners prefer Chicago to the "clutter and cutthroat" vibe of New York's Garment District. Here, he says, "Everyone wants to help elevate the whole industry and see each other succeed."
And he does mean everyone. Not only does Stock Mfg. Co. rely on designers to contribute patterns; it also asks customers to decide what they want to see made. Before each piece is produced, it’s put up for presale on the Stock website. If not enough people purchase it in advance, it will be scuttled. If it nabs enough votes, though, it's sold for a much more affordable price than your standard designer item.
The result so far is a catalog that consists of
their own line—an array of classic button-downs, bow ties, and pocket squares—as well as garments made in collaboration with designers, which tend to have a more unpredictable aesthetic. Right now, the crew is working with NYC-based
Feltraiger to promote a pair of slim chino shorts decorated with tiny American flags.
Of course, nothing makes it to the city's closets without the factory workers. When they aren't stitching a necktie by hand, they're operating intimidating machines that cut, sew, and press the garments. Here's a look at the process that takes a typical shirt from daydream to clothes hanger.
------------------------------------------------------------------------------------------------------
1. Design and Development
A designer who wants to work with Stock usually emails the company pictures of their garment. It's then up to the five owners to approve it. If they're drawn to the design, they ask for samples they can test for quality and fit. They also request a pattern, or what Jim calls "the puzzle of how you put the shirt together." A pattern comprises cutouts for all of the separate pieces of a shirt, such as the sleeves and pockets.
2. The Cutting Floor
Past the factory's library of patterns and samples lies the cutting floor. Here a worker lays a pattern out on marker paper, placing its components close together so as not to waste fabric. Sheets of fabric go underneath the marker paper, and they can be stacked quite high depending on how many shirts you want to make. Workers guide the cutter across the paper to slice all of the fabric into designated pieces at once. The process is a delicate one, especially considering the factory doesn’t use an automated cutter. “We do everything by hand,” Tim says, “so [the machine we use] has a knife that's constantly going up and down. It's very sharp ... [and] really heavy."
3. Sewing Rooms
Once all the pieces have been cut, they are tied together in bundles and taken upstairs via freight elevator. Each bundle holds only one part of the shirt, so you might be carrying a big pile of sleeves or collars. These components are given to the sewers. "Each operator does a different piece of the garment and passes it along, like an assembly line," Tim says, adding that experience is still key. "The majority of what we have are industrial single-wheel machines, and they're very fast. ... You have to be very careful—it's easy to overshoot your seams."
4. Specialty Machines
Not all of the machines up here look alike. Tim points to one that solely makes welt pockets. "I've sewn one by hand, it took me about half an hour. This does it in 15 seconds," he says. One of the owners’ favorite machines is a 100-year-old kick press. He explains how it applies rivets, grommets, and snaps: "You'll load up a bottom snap, a snap on the top, put your fabric in between, and just kick it." Different kinds of snaps or fabrics require different dies on the press, "and if it's wrong ... it's really bad."
5. The Finishing Touches
Finally, the shirt is pressed. Workers smooth out wrinkles on a flat surface, or they use a special form, a necessity for many uniforms. These forms look like incomplete mannequins and lend a pressed garment the correct shape in places like the collar and shoulders. From here, the clothing moves to quality control, where it's inspected and cleared for sale on the site.
------------------------------------------------------------------------------------------------------
In the future, the founders hope to expand and relocate to a bigger building. They're doing everything they can to raise awareness for their clothes in the meantime. They'll soon launch a series of designs made with fashion photographers and bloggers from New York, their first collaboration with non-designers.
When asked who they'd most like to see in one of their designs, Tim says "the Biebs." The joke is ironic, considering Justin Bieber is a fan of Feltraiger—the designer they're currently working with. Jim doesn't have a specific answer but is sure of his overarching goal. "Just people, in general. Not one person, a lot of people."